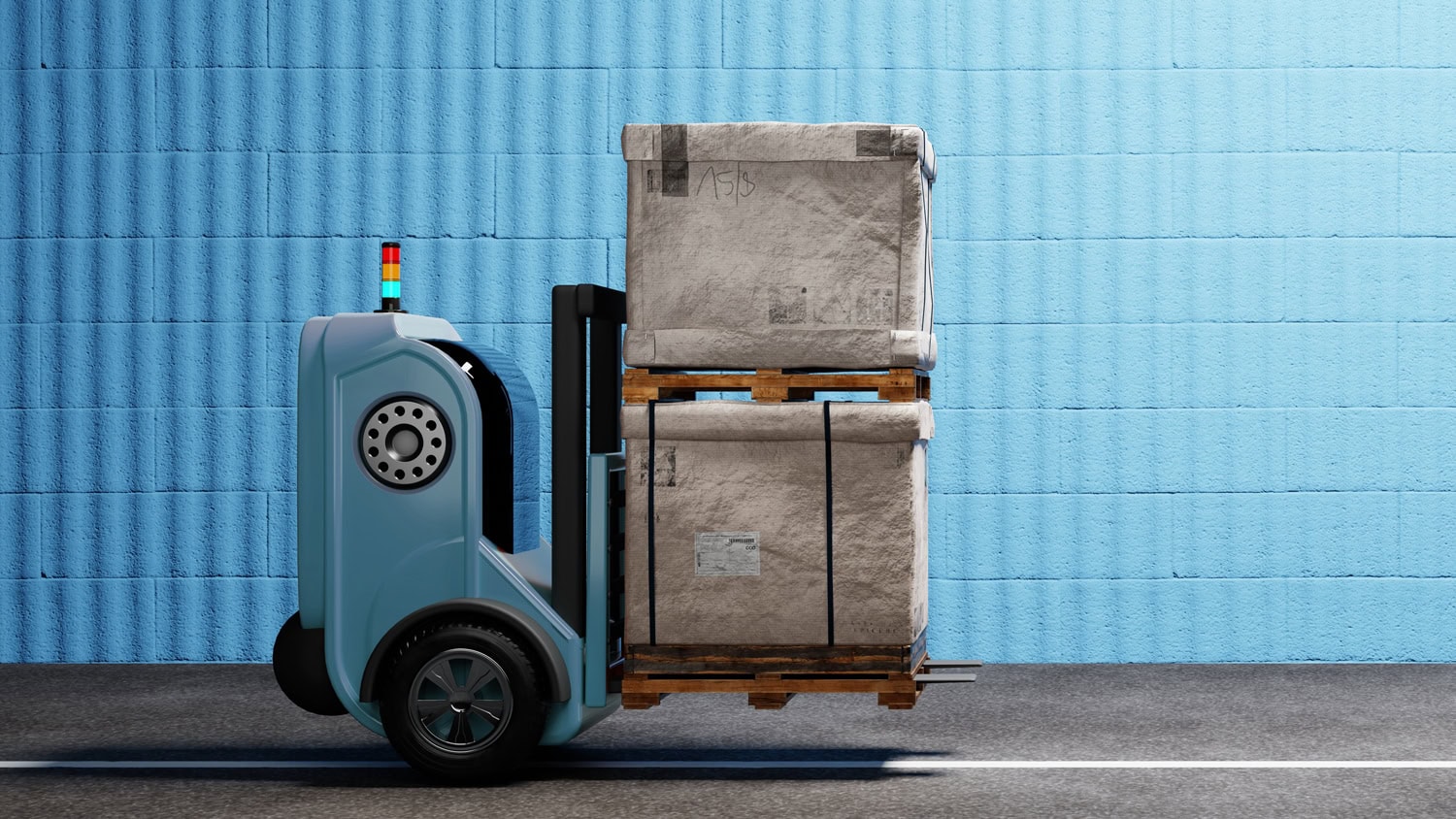
9 min read
The rapid increase in online shopping has spurred growth in fulfillment centers worldwide in the past few years.
The need for a safer workplace and faster turnaround time saw a 28% growth in 2021 in the warehouse automation market, including robots. Despite facing a possible economic slowdown in 2023, experts are cautiously optimistic about the long-term development of warehouse automation.
Types of vision technologies for warehouse automation
Scanning technologies have played a critical role in advancing warehouse automation by providing real-time visibility and accuracy of inventory data. The first commercial barcode scanning happened in 1974 in an Ohio grocery store where a pack of Wrigley’s gum was scanned for price. In the 1980s, the US Department of Defense adopted the Code 39 system labeling all goods sold to the US military. The adoption propelled the widespread use of barcode scanning in the industrial sector (source).
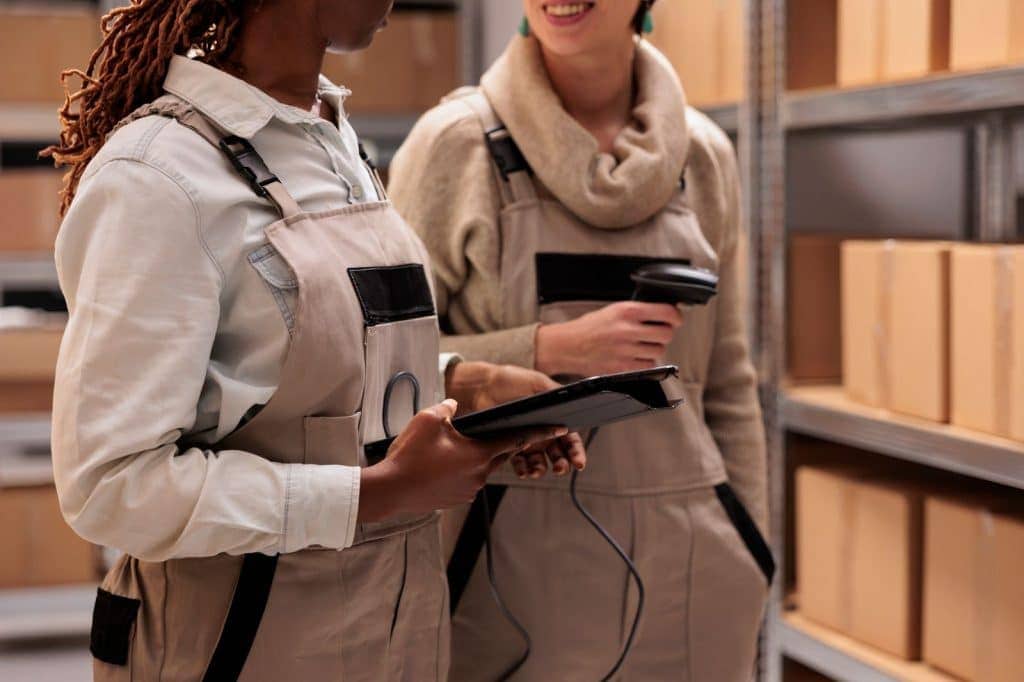
2D machine vision
One of the most revolutionary uses of scanning technology in warehouse automation history is using QR codes to store information. Automatic sorting systems direct parcels and goods down different routes using camera-based imaging scanners to decode the barcodes. Unlike traditional barcodes, QR codes hold more data and can be a unique identifier, as barcodes are reusable and meant only to identify product types. However, barcodes remain an integral part of warehouse logistics.
Modern warehouse automation utilizes many 2D machine vision cameras to perform tasks such as presence detection, integrated OCR (optical character recognition) scanning, or object detection.
About the Small Automation, Big Impacts series
The automation journey series is based on Hermary’s extensive field experience and many proofs of concepts we have worked on with our partners and end customers. We want to inspire the industry and help automation experts by sharing what 3D machine vision can do for them. As a whole, we will improve industrial automation together.
We want to hear about your journeys with industrial automation. Share your story with us, and we will make sure that it is published on our website for the whole industry to see.
3D machine vision on AGVs and AMRs
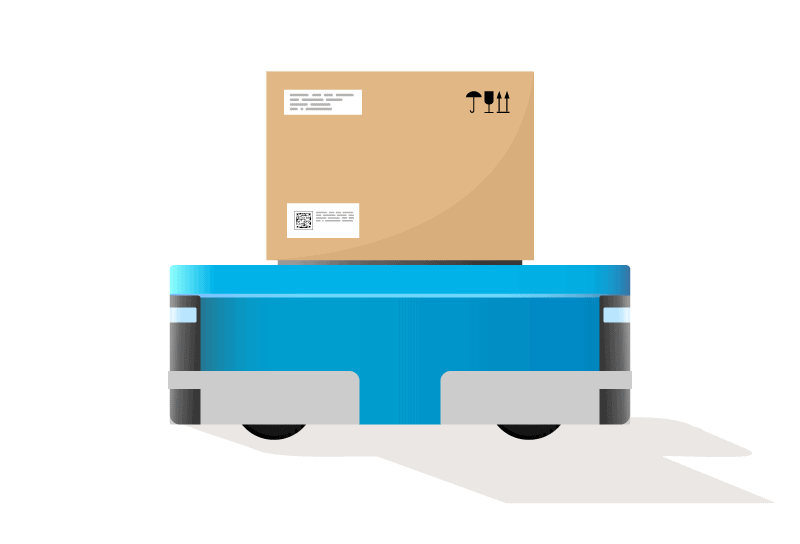
Traditional warehouses required workers to walk up and down aisles of shelves to pick products. Modern warehouses employ AGVs (automatic guided vehicles) to bring products to workers’ pick and pack stations. Eliminating workers from walking to goods significantly improved speed and efficiency. AGVs follow a predefined path with routes a software program plans to reach their destinations. Additionally, their onboard sensors and 3D vision cameras help them avoid collisions.
AGVs’ fixed paths can sometimes be inflexible and work best only in restricted areas with minimal human traffic. Unlike AGVs, AMRs (Autonomous Mobile Robots) can be equipped with robust navigation using SLAM (Simultaneous Localization and Mapping) algorithms with onboard 3D LiDAR or range finder cameras. This method helps estimate the robot’s position and orientation (localization) as it moves through the facility while the camera simultaneously creates a map of the environment. AMRs are more versatile than AGVs but require more computing power and may require additional infrastructural upgrades.
More automation opportunities for 3D machine vision
LiDAR cameras are commonly used onboard AGVs and AMRs as LiDAR is a type of Time of Flight scanning technology with a deep field of view. 3D triangulation, conversely, has a depth of field closest to the human eye, making them ideal for tight spaces or solutions requiring dexterity. The following areas are examples of automation journeys that can be enabled by 3D machine vision.
Volumetric dimension measurement
Whether at the receiving bay or shipping dock, modern warehouses rely on accurate volumetric data of the boxes to optimize storage spaces or palletizing options. Laser triangulation scanners are the ideal tool to capture these critical metrics as they have a fast scanning rate and accuracy down to millimeters.
2D camera vision relies on having “a good initial position of the camera relative to the object” to obtain data accuracy. For a shipping box to be scanned, the conveyor belt would have to be halted for a mechanical arm to push the box to be precisely within the camera’s field of view.
Conversely, two or more 3D laser scanners can be mounted above the conveyor belt to capture volumetric information in real-time without stopping the conveyor belt. The boxes’ orientation on the conveyor belt is irrelevant to calculating the dimensions. 3D vision scanners create a 3D representation of the scanned item in point clouds, which can be rotated in any direction using software algorithms. This feature is advantageous to streamlining and speeding up the inbound process. It also eliminates the need to re-orient boxes with a mechanical arm. Using 3D laser scanning to capture volumetric information is the best in warehouse automation because it is:
- Completely non-contact,
- Accurate down to millimeters, and
- Fast and continuous without having to stop the conveyor belt.
3D vision guided robots in hard-to-automate places
Industrial robots are articulated robots with multiple joints allowing them to move in a wide range of motion. They are designed to automate repetitive tasks that humans perform, making them ideal for tasks such as picking and packing.
3D scanners using laser triangulation have a depth of view similar to human eyes. However, its point separation can be down to 0.63 mm, approximately 2.7 times finer than human vision. Together with industrial robots, they are a practical automation solution, especially for strenuous tasks in confined areas or high-reaching spaces. Some areas where deploying industrial robots with 3D vision scanning will help streamline the fulfillment process are highlighted below.
Small Automation, Big Impacts is a collection of industrial automation journeys made possible by 3D machine vision.
We believe sharing these stories is a way to stay connected with our partners and positively impact the manufacturing community.
This free eBook also includes a bonus chapter to help automation professionals easily decide when to use 2D and 3D machine vision.
All this is just one click away in our new eBook, Small Automation, Big Impacts.
3D machine vision for accurate pick and place
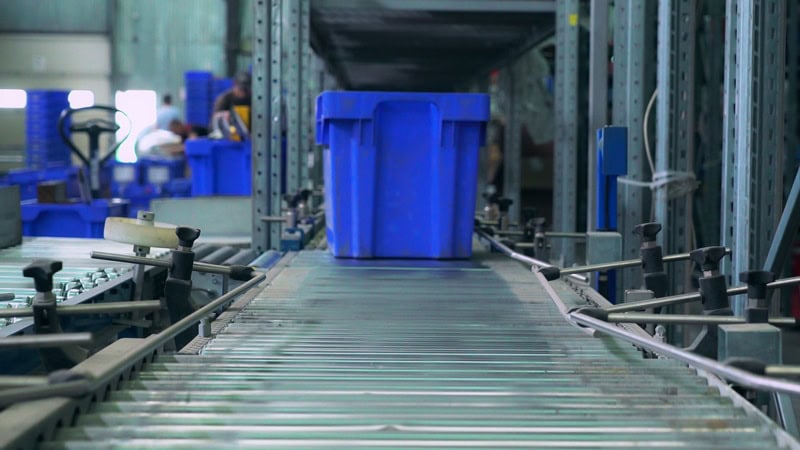
Outbound packages in a distribution center can travel a long way before being sent to their next stop. Workers make sure the shipping labels face the scanners by manually turning the boxes to the right side before reaching a checkpoint. Robotic arms and machine vision scanners can automate this repetitive and taxing task with artificial intelligence’s help. As with the sandwich assembly plant application, scanner data was used to train a convolutional neural network (CNN) model to recognize target objects’ features. Once the system is precise and accurate, it can process data from scanned shipping boxes on a conveyor belt. The system identifies which boxes must be flipped and sends their location (spatial) information to a robotic arm.
In many narrow spaces, humans still do most of the picking and placing. However, robotic arms with 3D machine vision can help. For example, in some parts of a distribution center, workers manually pick up packages from a chute and put them on a conveyor belt. This can be automated by using a 3D scanner to track package arrivals. The scanner data is used to calculate the package’s size and location so the robot arm can move into place and do the task.
Retrieving heavy items from high shelves can be unsafe for people. One way to prevent workplace injuries is by equipping robotic arms with 3D machine vision cameras. According to an editorial published by A3 (Association for Advancing Automation), industrial robots can have vertical reach as high as 4.6 m (15 ft). By outfitting these robots with 3D triangulation scanners, the robots move and stop at the correct spot in front of the storage shelf. The scanner also helps to visually verify whether the shelf is empty versus full before returning or retrieving the bin.
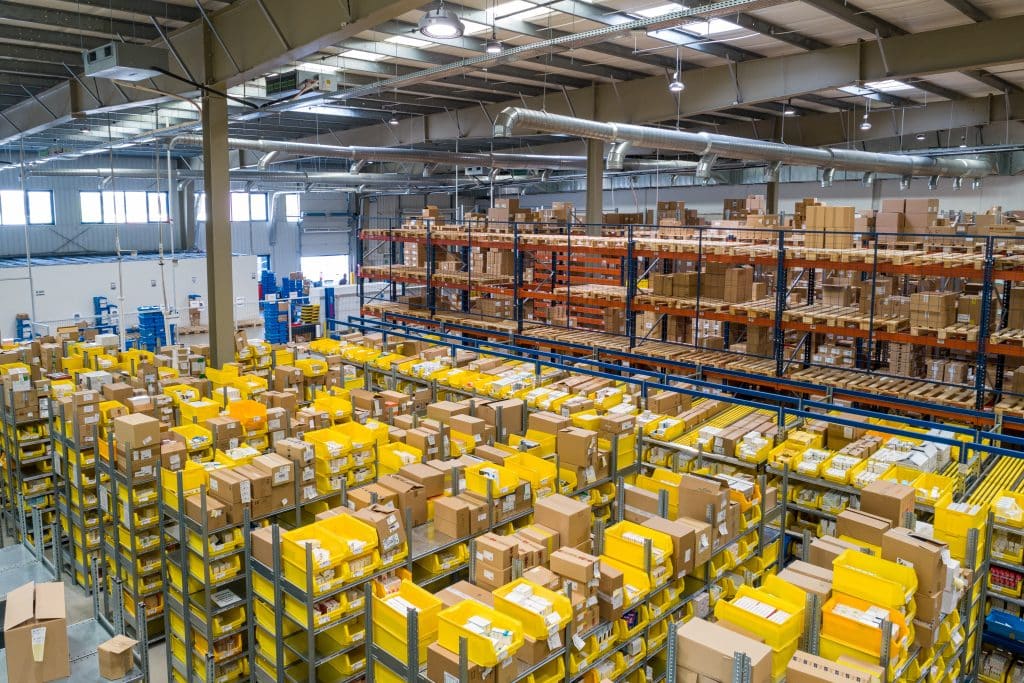
3D machine vision for handling large items
A 2021 Bain survey found that over 25% of consumers worldwide are now more likely to buy appliances online. By 2025, online sales are projected to make up 40% of all appliance sales. While warehouses use machinery to store large items, people still do many tasks manually.
The warehouse industry can learn from the sawmill industry’s digital transformation. Sawmills use 3D laser scanners to capture each log’s unique shape that optimization software uses to maximize the most out of each log and eliminate waste. Warehouses can use scanning tunnels with up to four scanners to scan large items to optimize storage space. Laser-triangulation scanners are fast and can generate up to 812,000 points of data per second. The result is an accurate digital representation of the item and an optimized storage plan for warehouses.
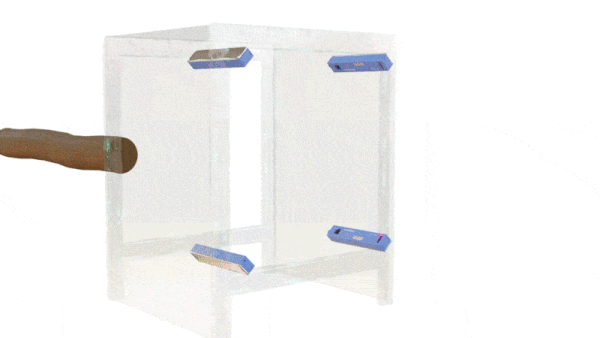
Integrating 2D & 3D machine vision on one platform
Vision technologies are crucial in warehouse automation, whether scanning barcodes or directing robots where to move. However, integrating all vision technologies into one platform can be complex since each device can communicate and be configured differently. One way to overcome this is to find vision devices that are interoperable with each other. Interoperability refers to the ability of different software applications and hardware devices to work together seamlessly.
Choosing cameras or scanners with vision standard certifications from A3 can make integration and communication between devices and the primary application more accessible. This, in turn, reduces the costs associated with developing and maintaining a vision system. As a result, this creates a win-win situation for system integrators and end-users.
Moreover, there is another significant benefit of using vision-standard certified devices: it prevents over-reliance on a single hardware or software vendor. For instance, utilizing GigE Vision-certified devices ensures interoperability, allowing solution developers to select from various vision vendors best suited for the job.
The journey continues
As online shopping continues to expand, warehouse automation has become essential for maintaining streamlined operations and high customer satisfaction. It is also vital for the well-being of current warehouse workers. According to a Harvard Business Review survey conducted in 2022, 60% of warehouse workers worldwide are optimistic about automation but would like their employers to provide more job security through reskilling and training.
Warehouse automation starts by finding the right solution partner
The warehouse automation journeys are long and require careful planning, but many lessons can be learned from other industries. The digital transformation of the sawmill industry highlights the importance of finding the right automation partners. In this case, a qualified system integrator specializing in warehouse automation. Warehouse automation is an integrated workflow that includes software, hardware, people, and processes, and an experienced system integrator can help companies find the right balance among all four parties. In addition to integration, system integrators provide ongoing support and maintenance services, ensuring the automation system operates reliably and efficiently over its entire lifecycle. The Control System Integrators Association (CSIA) is a good resource to start the search. The website offers a directory of companies specializing in automation for warehouse management or materials handling to find a qualified automation partner.
Finally, the collaboration between 3D machine vision and industrial robots has the most potential in automating repetitive tasks that require agility and precision. Companies that have already started down the automation path are encouraged to monitor their processes. The continuous optimization of automation will help businesses improve efficiency and simultaneously create a safer workplace for their employees.