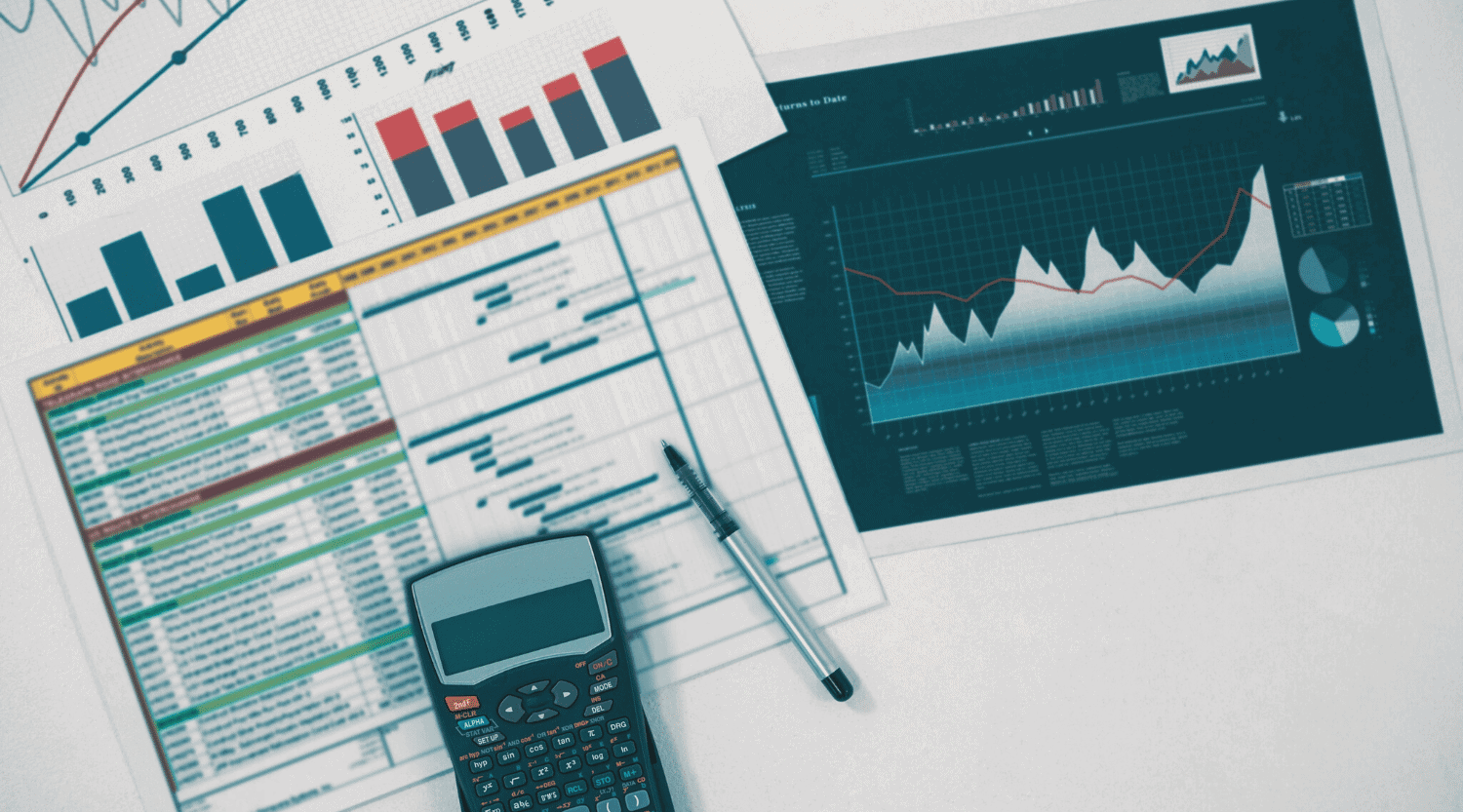
8 min read
As manufacturing moves into the Fourth Industrial Revolution, companies must evolve to meet new OSHA guidelines and attract young talents.
The processes that used to work will become increasingly challenging to meet customer demands as unified goods give way to personalized products. The decision-making is further slowed down by the lack of real-time data, creating an even wider chasm between production supply and market demand. The recent advancement in manufacturing technology has made reshoring a profitable strategic move, paving the way for more greenfield projects to come.
Traditionally, automation projects are primarily evaluated and approved based on the return of investment (ROI). A higher ROI value can indicate a higher projected return on capital expenditure (CAPEX). However, automation projects are long-term assets, which means the ROI calculation overlooks the operating costs associated with the purchase.
Don’t start an automation project until you read this
Get the free eBook that lets you —
- Avoid unexpected costs like energy or maintenance
- Future-proof your manufacturing facilities
- Know what to watch out for when managing automation projects
- Own the tried-and-true 23-point checklist on choosing the right System Integrator
Let’s talk about the Total Cost of Ownership
This multi-part article dives into what automation experts use to guide them through project management. The total cost of ownership (TCO) evaluates a project’s long-term value instead of the initial cost. It is a robust system that includes a project’s multifaceted aspects, such as energy consumption or user experience (UX), as evaluation criteria. Ultimately, it helps the project management team uncover hidden costs that may balloon over time, which the traditional ROI method failed to account for. Most importantly, it helps the team make the right investment decisions and realize hidden savings in the long run.
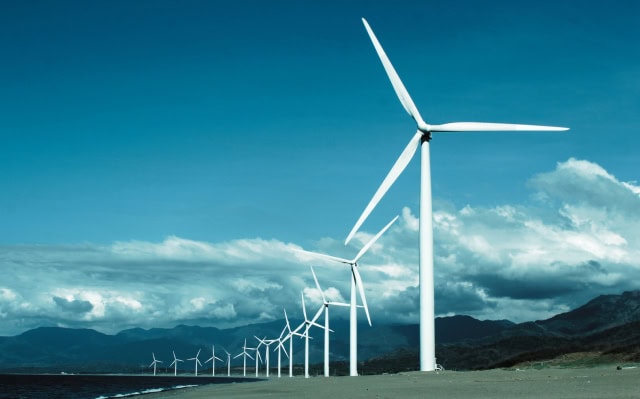
How efficient is your energy?
Choosing energy-efficient components or systems is often met with resistance because of its high initial investment. However, it is wise to select an energy-efficient solution from a financial standpoint as energy is becoming scarcer. Its price globally is forecasted to rise by 35% in the next 15 years. Policymakers in various parts of the world are implementing tighter regulations on greenhouse gas (GHG) emissions by imposing carbon taxes on companies to help reduce CO2 emissions. In particular, companies in energy-intensive industries, such as food, pulp and paper, chemicals, steel, and metal, will need to incorporate progressive energy-saving measures.
The many hidden savings from a greener energy source
From an operations point of view, energy efficiency is a strategic winning factor that applies to all modern factories. A case study done by McKinsey found that in Germany, energy-conscious companies who choose more precise and faster automation systems reap the benefits of having superior system flexibility and shorter changeover and ramp-up times. An ongoing study by the International Energy Agency (IEA) also corroborated McKinsey’s findings. IEA concluded that the added value from industrial energy efficiency measures is 2.5 times the energy savings. Lung, Nimbalkar, and Wenning’s 2019 research paper summarized the many benefits from such efforts:
Operations and Maintenance
- Reduced maintenancecosts
- Reduced purchase of ancillary materials
- Reduced water consumption
- Lower cooling requirements
- Reduced labor costs
- Lower costs for treatment chemicals
Production
- Reduced product waste
- Increased production
- Improved product quality
- Increased product reliability
- Shorter process/cycle time
Work Environment
- Increased worker safety
- Reduced noise levels
- Improved workstation air quality
Environmental
- Reduced hazardous waste
- Reduced dust emissions
- Reduced waste water output
- Reduced CO, CO2, NO2, SO2 emissions
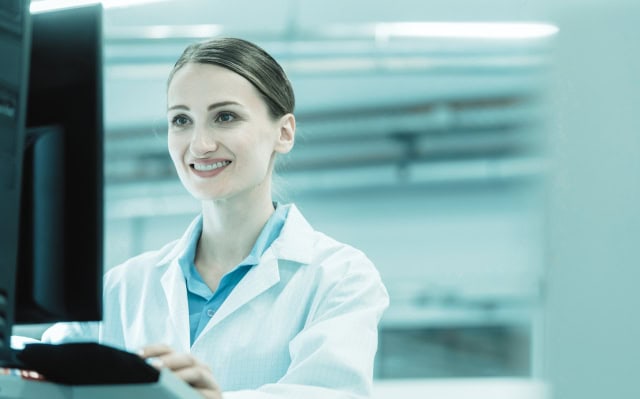
User Experience (UX) is not just for consumer products
Make no mistake, manufacturing will move to incorporate more human talents in the future as Industry 5.0 ushers in a tighter machine-human collaboration. Forward-thinking companies see the long-term benefits by investing in Human Machine Interface (HMI) with good user experience (UX) designs. HMI is integrated hardware with software designed to help human users control and monitor machinery and production lines. UX is a discipline that aims to develop an intuitive environment that allows users to accomplish what they set out to do with the least amount of effort possible. It aspires to provide positive user experiences, thereby increasing the overall usability of the system. The International Organization of Standardization (ISO) dictates that a system’s usability should measure its effectiveness, efficiency, and satisfaction.
Realize hidden savings through graphical data representation
Manufacturing employs a diverse group of people in their workforce. Many facilities also span more than three continents. One plant manager revealed at least seven languages other than English are spoken on the shop floor just within his facility. A good HMI design constitutes a Graphical User Interface (GUI) or icon-based interface that interacts with operators through visual representation. GUI is significantly easier for workers to use than the traditional interface design that toggles between different languages.
Not only does GUI lower the language barrier, but younger generations entering the workforce are also familiar with manipulating devices through GUI. Experienced UX designers strive to create a user-friendly interface that communicates as clearly as Ikea’s award-winning instruction manuals. An intuitive design like this significantly reduces the learning curve, saving valuable time and resources in training.
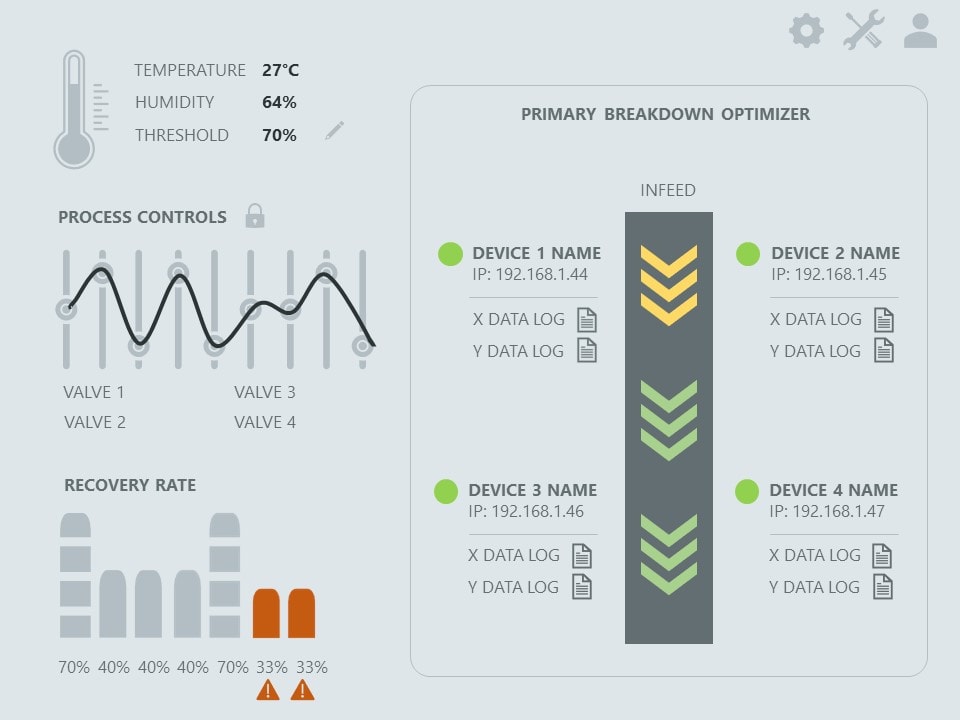
Companies that invest in industrial automation UX design also focus on reducing the operators’ cognitive load. Industrial UX design is different from a consumer-facing interface (such as an eCommerce site). An operator works closely with these monitors for eight to ten hours during their shift. Redesigning to cater to their use cases can reduce the workers’ visual and mental fatigue, which goes a long way to boost their job performance. According to research published by the American Society for Engineering Education and UXMatters, the following best practices can significantly improve manufacturing workers’ user experience.
- Reduce visual noise. Background images or decorative elements on the screen should be removed as they do not add any value. Only contextual information that helps operators quickly understand the system’s health should be displayed, and
- Grayscale should be the primary choice of color swatches and only use colors (e.g., red, green, or blue) to highlight areas that need users’ attention, and,
- A graphical representation of the process helps users quickly understand and monitor the system. However, a photo-realistic or a rendering of the system should be avoided as it only creates clutter and slows down the human comprehension process.
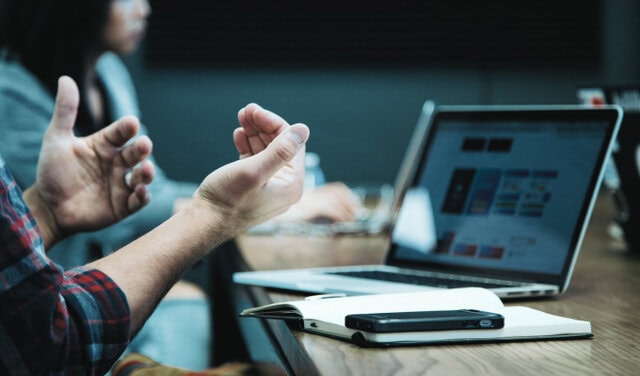
Data acquisition and analysis are the keys to optimizing manufacturing processes
Technology adoption in manufacturing in the current business landscape is imperative. To strengthen competitive advantages, modern firms must examine the digital data they collect and create actionable intelligence. McKinsey’s 2021 case study on the pulp and paper industry’s value chain illustrates how data can improve operation in the following three areas:
- Automation and robotics. The broadest application of industrial data collection is executed so that repetitive tasks can be automated and robotics can “see.”
- Digitizing end-to-end processes. A comprehensive digital transformation (DX) plan will create value for the business, supply chain, and customers. This means streamlining the value-creating process by automating certain decisions based on real-time data.
- Advanced analytics for optimization. The most practical use of data is analyzing it to find the best possible outcome for KPIs such as process performance, production yield, quality control, value generation, and more.
Mining the data for hidden savings
In the McKinsey case study mentioned above, the pulp and paper industry reported up to 10% of throughput gain by optimizing processes with data analysis. Inexplicably, the entire value chain benefitted from reduced material usage and energy consumption, representing an opportunity of up to 6 billion dollars in the US alone.
This case study on the digital transformation journey of the sawmills also proves how high-precision data became the pillar of a sawmill’s competitive advantage. Both the Edging and Trimming processes in a sawmill are designed to maximize the recovery of raw material. So when 3D laser scanning and Point Cloud data were integrated to automate both steps, not only did it help to eliminate human subjectivities, they dramatically improved the sawing precision and accuracy. The automation project gave sawmills the confidence to cut closer to the target sizes (as timber will shrink in the subsequent drying process) and upgraded to thinner saw blades to reduce the non-value-added sawdust. A typical sawmill adds $200,000 to its net profit annually by reducing the target sizes by 0.01 inches.
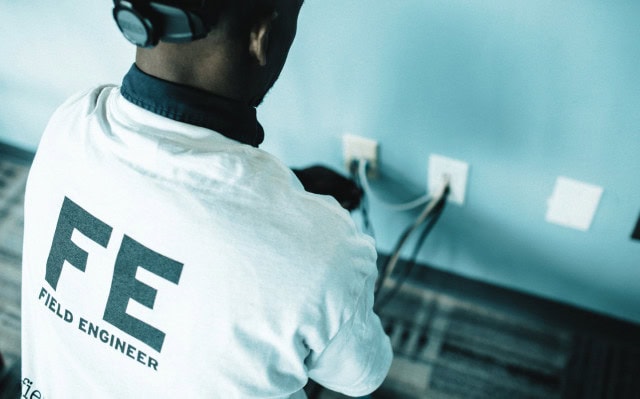
Personnel training to encourage broader technology adoption
A forecast by S&P Global shows that North America’s industrial sector is expected to see a jump of 12.4% in CAPEX by the end of 2021, mainly due to pent-up consumer demands and reshoring manufacturing companies. Whether it is a brownfield project that upgrades existing systems or a greenfield project that designs a production line from scratch, companies must outline a learning and development (L&D) program to facilitate positive technology adoption by the employees.
The time and effort needed for operators to become confident in operating a new system is an indirect cost that often goes unexamined in the traditional ROI method. However, choosing one project proposal over another for having a shorter training period is shortsighted. The project management team should engage with HR to co-own the training programs to paint a complete picture. Together, they can take inventory of employees’ existing skills, define learning outcomes and prioritize subjects to design courses accordingly. The Manufacturing Institute and American Psychological Association’s study shows that 69% of employees 25 years or younger strongly agree that an ongoing training program that teaches them new skills and develops their careers is a powerful incentive to stay with a company.
More hidden savings when using the right technologies
Seasoned project managers and HR experts know that durable, transferable, and in-demand skills are worth designing training courses for. This means adding value to employees’ work by educating them on standard and widely-used skills in industrial applications. For example, when a national meat processing plant automated one of its critical sawing processes, it upskilled its Production Operators. By equipping them with basic Point Cloud skills, the employees uncovered a more cost-effective way to process certain cuts. The unique insights led the company to deploy more vision-aided meat saws with confidence and success.
Cultivating experts by integrating the right technologies
Personnel training is also a substantial financial consideration for a System Integrator (SI) whose responsibilities include developing interfacing software so that hardware components can communicate with each other. Experienced SI’s partner with component vendors or suppliers who use proven technologies or whose products have a long service life. These well-designed components use standardized programming codes and follow industry guidelines, meaning the integration engineers can easily and quickly reapply the product training to different projects and applications.
Furthermore, as integration engineers accumulate more practical experience over time, they become the team’s Subject Matter Experts (SMEs). These SMEs possess product knowledge invaluable to the field engineers who provide system maintenance or the shift managers who need to troubleshoot. Their expertise eliminates the need to relay messages back to the component or software provider. Such timeliness translates to a shorter changeover or idling time, saving the manufacturer a tremendous amount of loss of production value.
In the next installment of the article, three more criteria will be examined to guide automation experts to maximize CAPEX projects and avoid potential financial pitfalls. To receive updates on The Hidden Numbers in Automation Projects, subscribe to our newsletter or follow us on LinkedIn.